Liquid storage container failures can easily turn into serious accidents. That’s why business owners need to focus on quality, when choosing the appropriate liquid storage equipment. Cheap alternatives that don’t comply with industry regulations, shouldn’t even be considered. Fortunately, in the last few decades, liquid container manufacturers have made a huge progress, especially in the areas of engineering design, coating processes and field construction techniques.
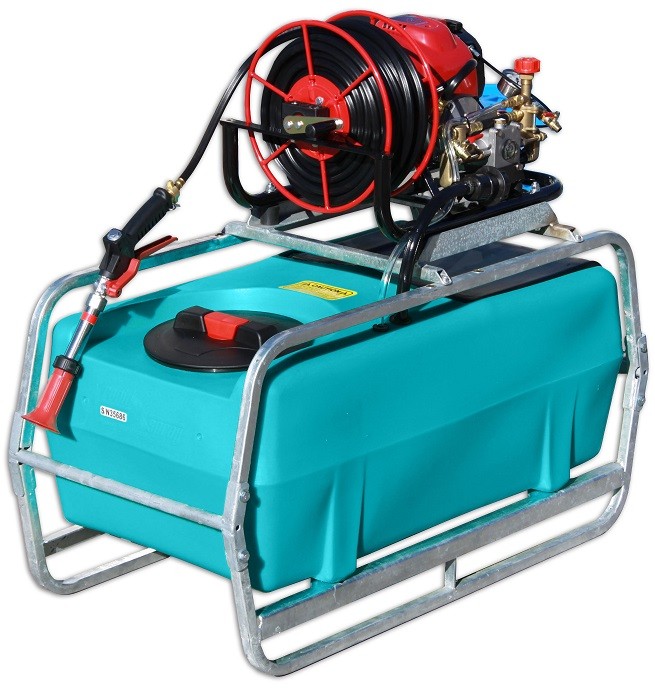
Liquid container selection process
The container market has been growing at a very fast rate, which means that business owners now have more options to choose from. The selection process should always start from field requirements. Business owners should inspect the place where the tank will be stored and define the list of important value aspects (attributes). Depending on the type of business and the liquid that’s going to be stored inside, value aspects can range from low maintenance and cost efficiency to special sizes, shapes and types of coating.
Important considerations
Before they choose an appropriate container, business owners need to determine whether its application will be a routine one, or it’ll require special some conditions. The easiest way to do this, is by checking the list of important application considerations and seeing whether some of the following criteria represents a concern:
- Container’s capacity requirements in cubic meters or liters;
- Special project design conditions and compliance with industry standards and codes;
- Unique requirements for liquid storage (pressure, agitation etc.);
- The necessary temperature and the PH value of the stored liquid;
- Types of construction materials that should be used;
- System requirements;
- The container’s shape and configuration type (flat or sloped bottom, elevation etc.);
- Anti-corrosive protection;
- Foundation requirements (concrete slab or ring, steel foundation with external saddles etc.);
- Warranty, maintenance and other types of guarantees;
If some of the criteria on the list represents a concern, business owners should contact a liquid storage application specialist, who will advise them on choosing the correct container and on designing and preparing their lot for easier application. If they hire a container specialist, their role in the selection process can be narrowed to reading customer reviews and checking containers’ prices.
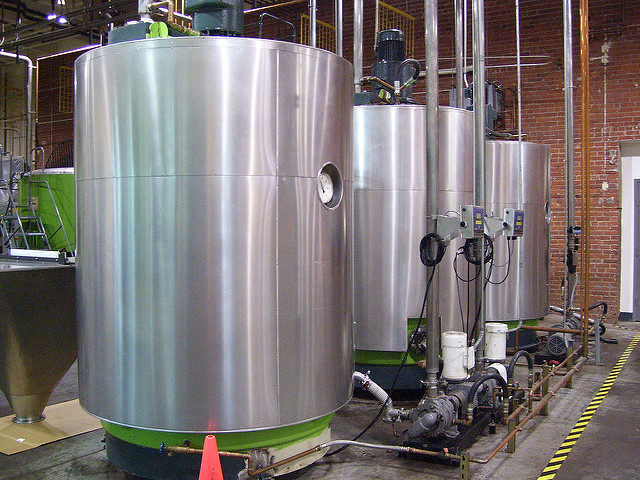
Types of containers
Liquid storage applications either come with a shop-welded or a smooth-wall bolted tank. Business owners can also choose between four different construction designs, including:
- Concrete;
- Field-weld;
- Hybrid;
- Bolted RTP (rolled, tapped panel);
These tank designs are used for both industrial and municipal applications and hybrid and field-weld containers are considered to be the most cost-efficient.
Liquid storage containers can also come with special add-ons, depending on their purpose. The containers used for municipal water supply come with regular taps, while the containers used in agriculture come with special hatches, mouths and pipes through which they can connect with sprinklers, contemporary boom sprayers and other irrigation equipment.
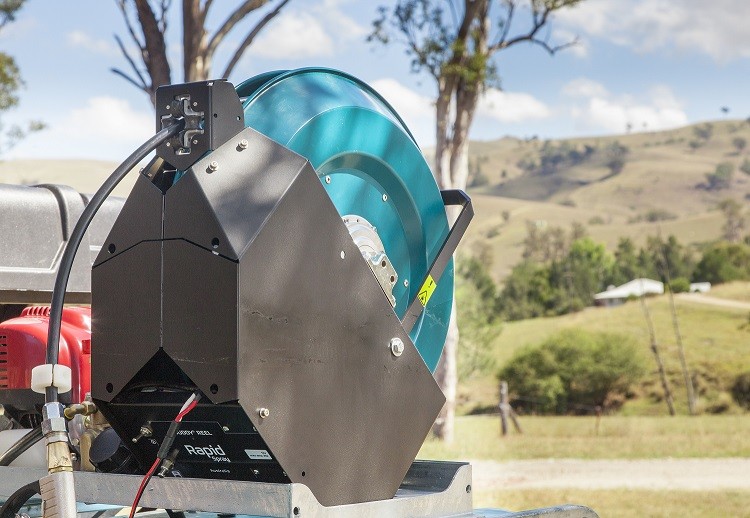
Good tank installation practices
After comparing the value attributes with life cycle and installation costs, business owners will be able to choose an appropriate tank and start with the application process. During this process they should take these facts into consideration:
- Water or wastewater tanks below ground should have a concrete construction and an aluminum dome cover;
- Tanks built above ground should be installed on steel or concrete bottom and they should have a steel construction and an aluminum dome cover;
- Bolted tanks should come with a bolted RTP construction, steel or concrete bottom and aluminum dome cover;
- Field-welded tanks should come with a field-welded tank sidewall construction and they should have an aluminum dome bottom;
Most modern of these tanks guarantee years or even decades of trouble-free liquid containment. Across the world, you can easily find steel containers that are more than one hundred years old and they still haven’t leaked or shown any signs of corrosion. In this day and age it’s impossible to imagine a disastrous accident caused by a leaking tank, like the Boston molasses disaster from 1919. Still this and many other incidents caused by negligence and faulty containers should remind us that we need to take liquid container selection very seriously.